Fatigue
Ashes provides a workflow for automatically gathering relevant stress series during simulation, applying stress concentration factors, then performing rainflow counting on the resulting stress series. Finally, lookup in S-N curves is performed to arrive at the total fatigue damage and lifetime of each construction detail. This section will describe the workflow for performing fatigue analysis in your simulations.
1 Joints
In order to peform fatigue analysis, the model must specify a set of Joint definitions. A joint specifies which members (elements) are to be designated as chord and brace members.
Selecting Support structure | Support structure type | Tubular tower on truss tower will produce a truss tower with all joints created. To follow this workflow yourself, you can use such a model. Exporting the truss tower to file will give a file that contains Joint definitions, to use as a working example.
1.1 Geometrical definition of tubular joint
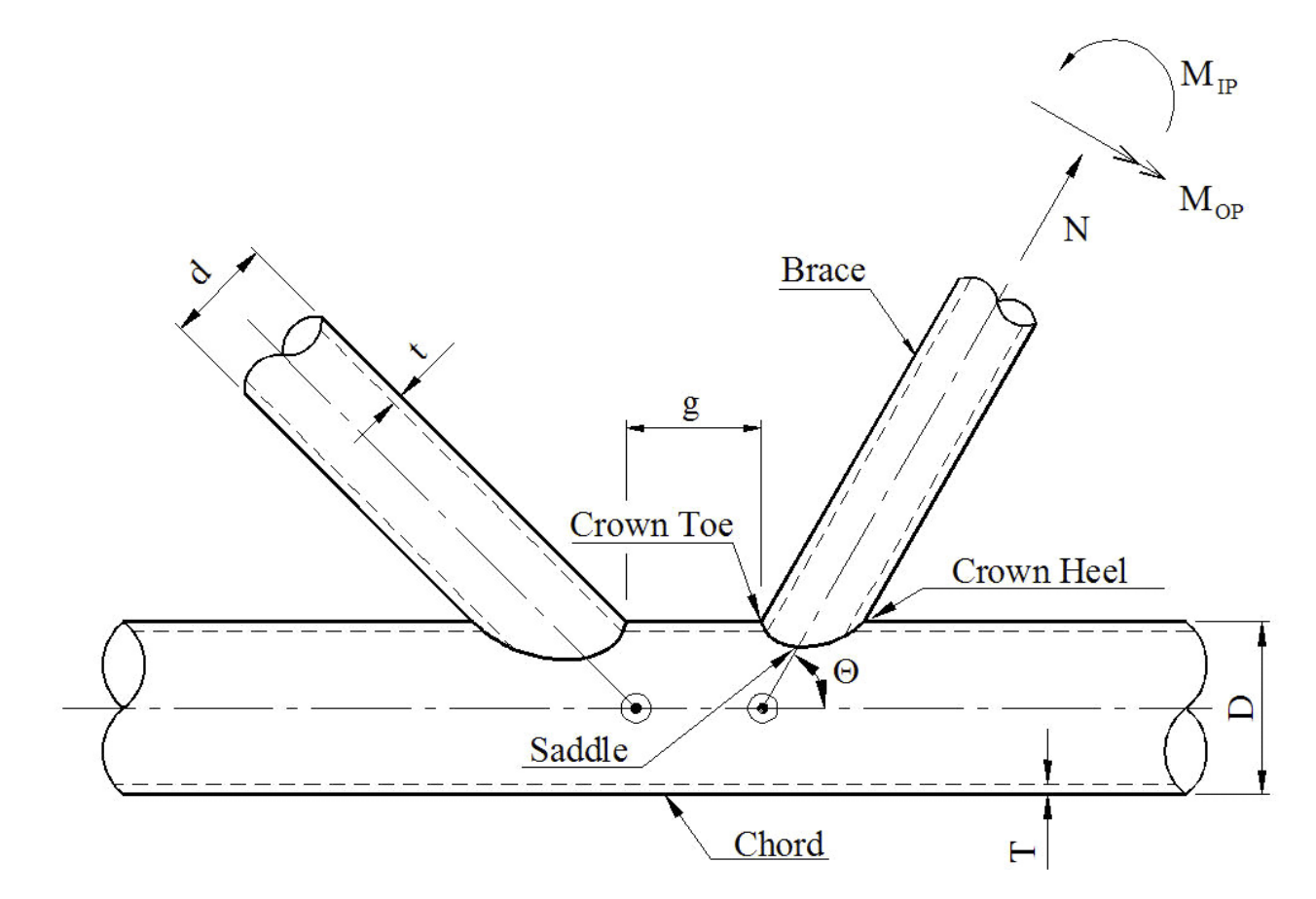
Geometrical definition of a tubular K joint, showing directions of forces, saddle and crown points and various dimensions.
1.2 Joint definitions in support section text file
Joint definitions are placed in the section titled Joints.
1
2
3
4
5
Joints
# Joint name Chord elements Brace elements
4-A 3&4 36&39
4-B 3&4 188&191
7-A 6&7 44&47
Example of joint definitions in support section file
A joint should only have braces that lie in the same plane. If there are multiple brace planes, one joint must be specified for each plane.
1.3 Selecting a Joint and viewing information
Joints are visualized in a blueish color covering the chord and brace members. To view its properties, you can right-click the joint.
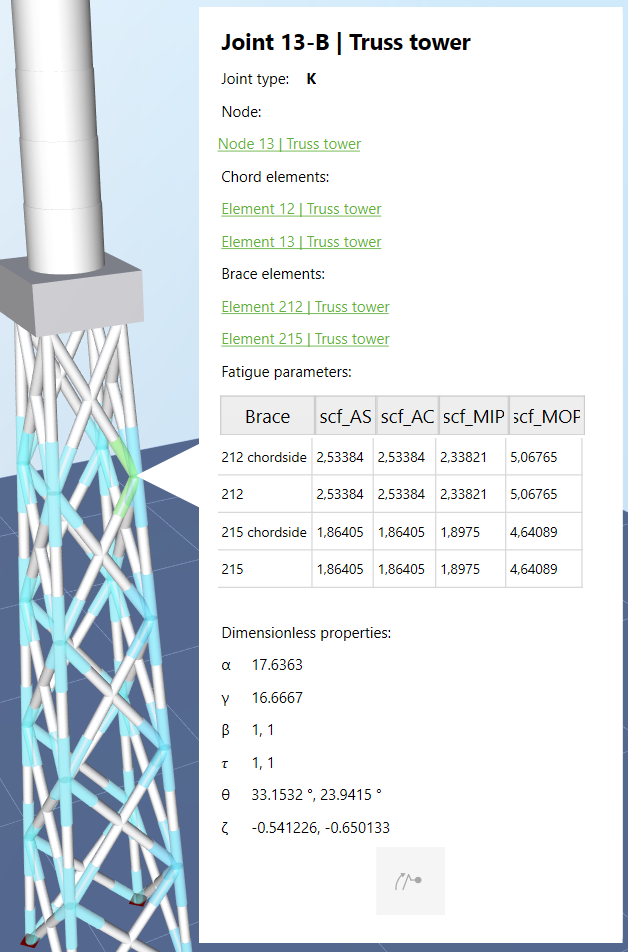
Joint information window (for tubular on truss tower), accessed by right-clicking a Joint.
2 Stress calculations
2.1 Stress concentration factors (SCFs)
For fatigue computations, the nominal stresses (as seen in Beam element sensor) are multiplied by factors which depend on the geometry and loading of the joint. Ashes uses formulas from the DNV-RP-C203 recommended practice.
SCF index | Factor is used for |
AS | Axial stress at saddle points |
AC | Axial stress at crown points |
MIP | Moment/bending stress in-plane (crown points) |
MOP | Moment/bending stress out-of-plane (saddle points) |
2.2 Hot spot stresses
Stresses are computed at 8 hot spots at the intersection between the braces and the chord. A superposition of axial stress and bending stress (in-plane and out-of-plane), each multiplied by the corresponding SCF gives the effective stress used for fatigue.
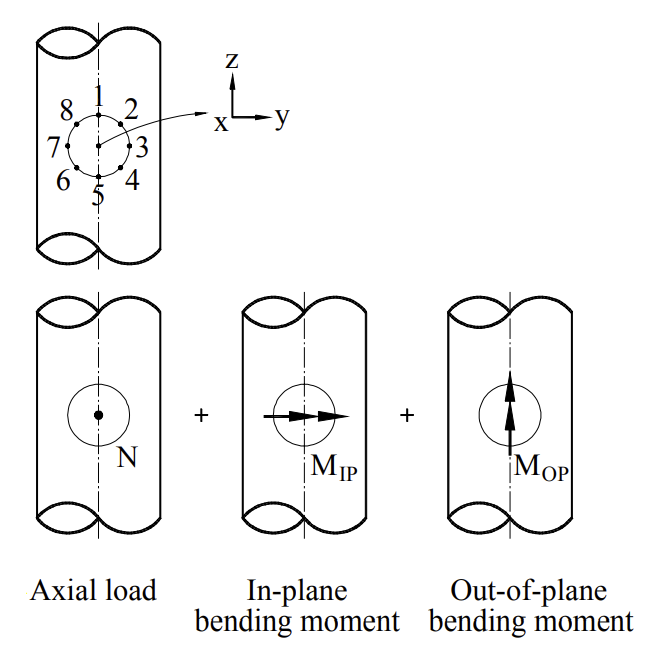
Hot spot stress points and directions of forces.
The fatigue sensor names stress points according to their angle, as shown in the table below.
Hot spot | Field name in fatigue sensor |
1 | Stress pt0 |
2 | Stress pt45 |
3 | Stress pt90 |
4 | Stress pt135 |
5 | Stress pt180 |
6 | Stress pt225 |
7 | Stress pt270 |
8 | Stress pt315 |
2.3 Classification of joints
Different SCF equations are used, depending on the classification of the joint. The classification of a joint (Y, K, X) depends on its geometry, but also on the actual loading of each brace. Ashes will automatically determine the classification of each brace every time step during simulation and apply the corresponding SCFs. For example, if a brace is determined to be 50 % Y and 50 % K, the effective SCF used will be 50 % * SCFY + 50 % * SCFK .
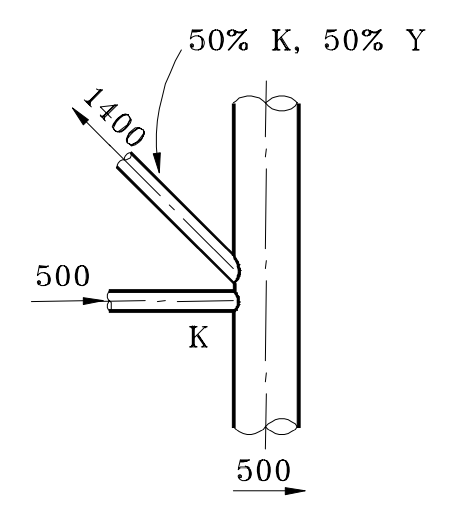
Example of a joint where one brace is classified as a mix of K and Y due to the actual loading.
3 S-N curves
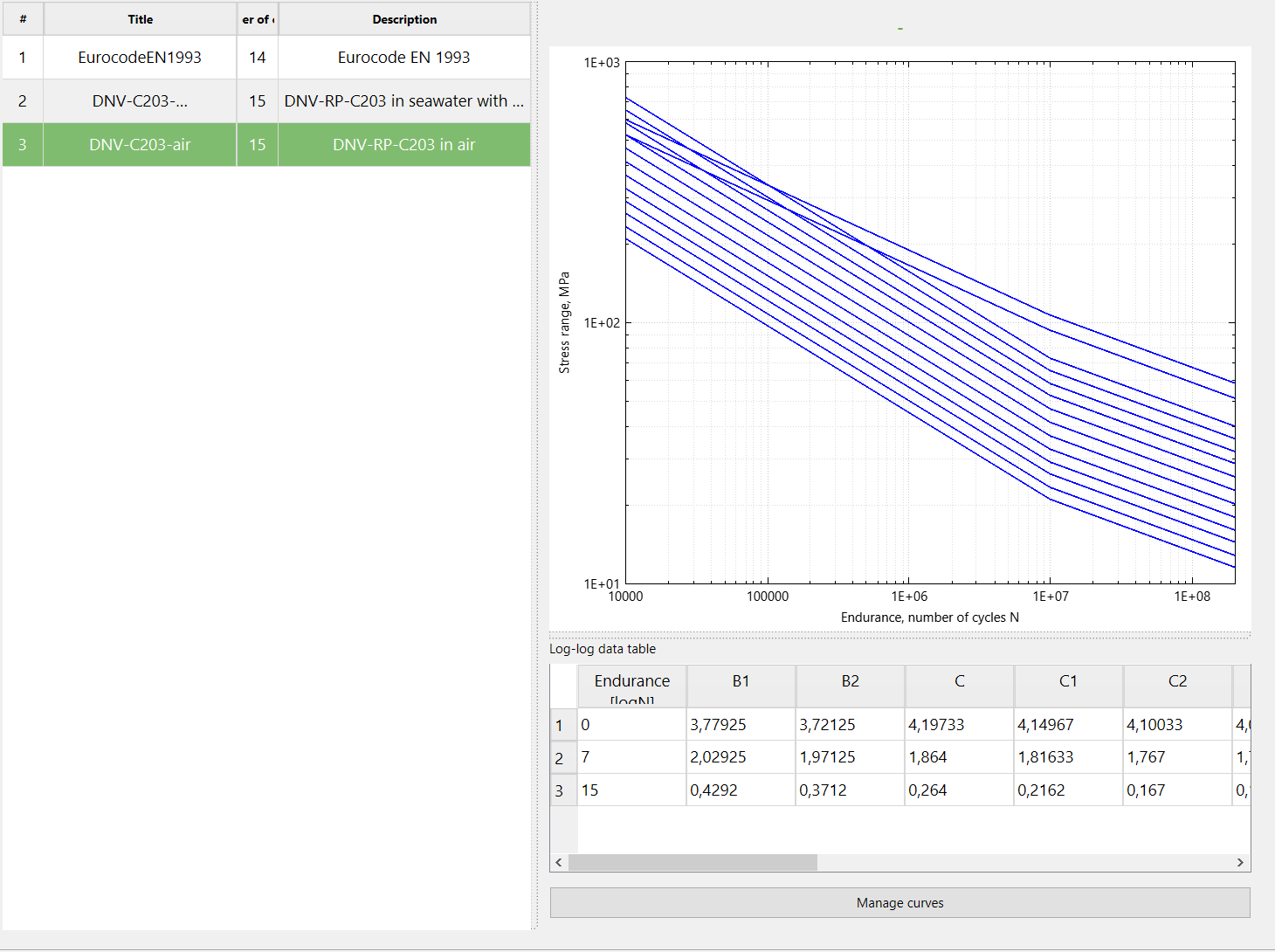
Ashes comes with a set of S-N curves. This window is found by going to Preferences | Fatigue | S-N curves...
3.1 Assigning S-N curves to joints and sensors
Default S-N collection and category are set in Preferences | Fatigue. All joints and fatigue sensors will be set to use these defaults when they are added.
The S-N collection and category to be used for fatigue computations can be assigned individually to each joint or sensor. To assign a sensor, right-click the sensor, select Options and change the settings in the opened dialog.
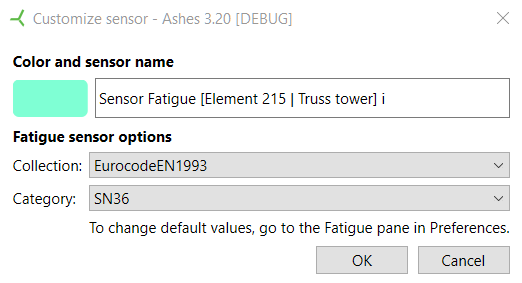
Dialog for assigning S-N curve collection and category to a fatigue sensor
S-N curve and category can also be specified per joint when importing from file (not implemented yet)..
4 Workflow
A more detailed explanation of the workflow is given in the Theory Manual, in the Fatigure analysis procedure document
4.1 Relevant settings and parameters
Analysis parameters | Analysis | Misc. | Fatigue calculations start time specifies at which simulation time fatigue calculations should start. Usually, initial transients should be excluded. To achieve this, set this parameter to e.g 30 seconds.
4.2 Workflow summary
- Define Joints. Specify each joint to be included in fatigue computations in the Joints section of the support section file, then import it (this is only required if you perform a fatigue analysis on a truss tower).
- Add sensors. Right-click each joint and click the Add sensor button. For joints, this will produce two sensors for each brace, one for stresses chordside and one for braceside. If you want to add a sensor for every joint, click
in the Sensors window and choose Add fatigue sensors to all Joints.
- Assign S-N curve and category. Each sensor will be assigned default S-N settings when they are added. To change these settings, right-click the sensor and choose Options. Default S-N settings can also be assigned per joint in the Joints section of the support section file.
- Run simulation(s). Run your simulations, either in Time simulation or in Batch. The fatigue sensors will collect stress ranges for each hot spot during simulation.
- View report. If you run in Time simulation, you can generate the fatigue report by clicking
in the Sensors window and checking the Generate fatigue report...option. If you run in batch, there will be report PDF file called Jointssummary.pdf placed in the results folder.